References
Water/Sewage Treatment
Modernisation of phosphate elimination ensures efficient wastewater treatment at the Linkenheim-Hochstetten wastewater treatment plant
Project location:
Linkenheim-Hochstetten (Germany)
Date:
2024
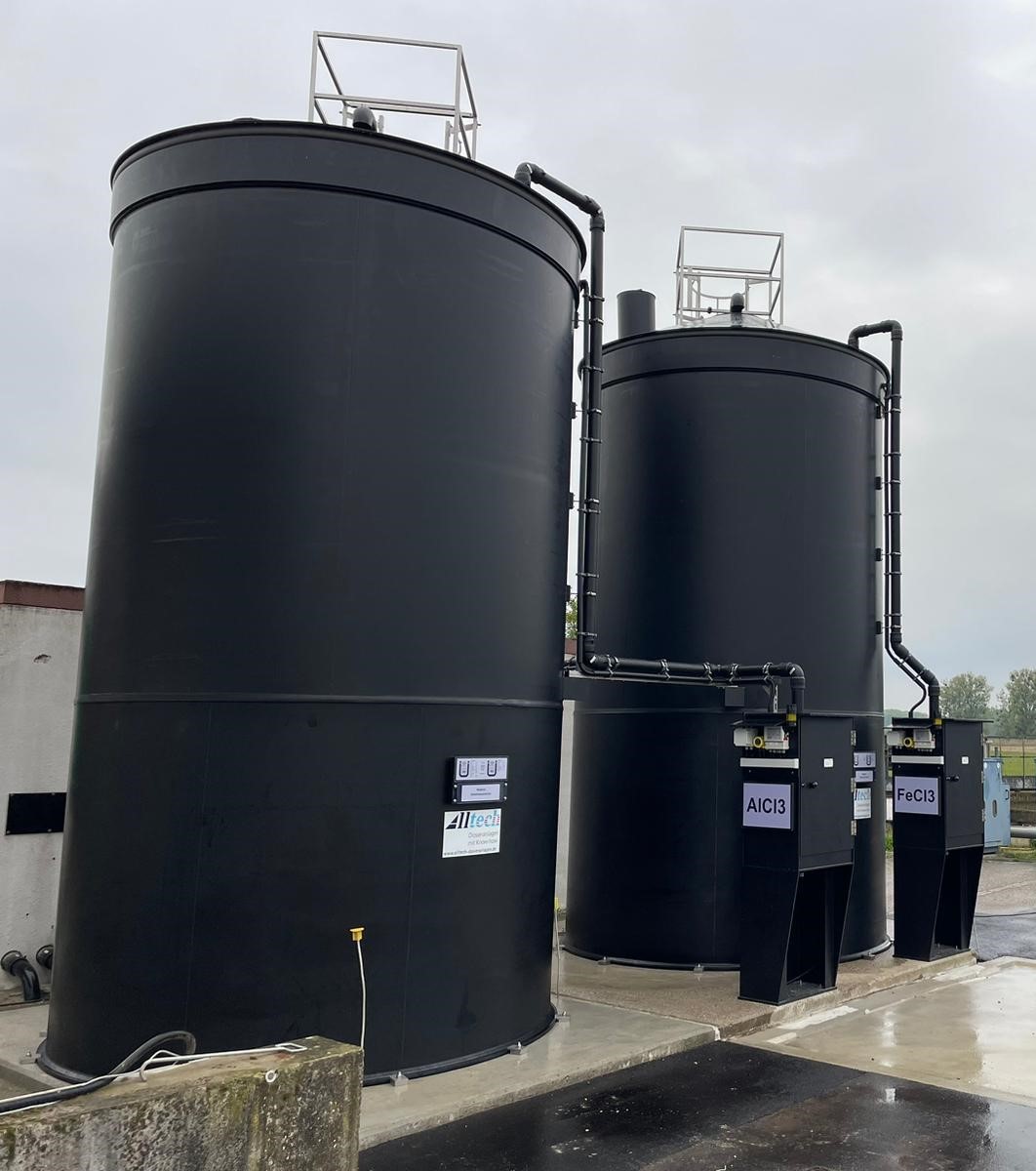
Storage tanks for chemicals
System used:
Two chemical storage tanks for outdoor installation with a net volume of 25 m³ (designed in accordance with WHG, TABESY tank filling system, dosing station with four FKM piston diaphragm dosing pumps with iReg intelligent control system
Description:
With a population equivalent of 15,000, the Linkenheim-Hochstetten wastewater treatment plant is one of the larger wastewater treatment plants (size class 4). In order to safely and efficiently comply with the discharge values for phosphorus applicable to size class 4, the municipality invested in the modernisation of P elimination.
Flexible use and safe storage of two different chemicals
Two PE storage tanks, each with a net volume of 25 m³, are used to ensure that sufficient precipitants are available at all times. Aluminium chloride and iron (III) chloride are used as precipitants. The storage tanks are insulated and heated for outdoor installation. They are designed for earthquake zone 1 and designed in accordance with the regulations of the Water Resources Act (WHG: Wasserhaushaltsgesetz) and have a type approval from the DIBt (German Institute for Building Technology: Deutsches Institut für Bautechnik).
Access ladders and a platform are mounted on the storage tanks for inspection access – all designed in accordance with the relevant safety guidelines (DIN EN 14122).
The chemical storage tanks are filled using the TABESY tank filling system, which enables safe filling via tank lorries.
Individual dosing pumps with intelligent iReg control for four dosing points
The dosing of the chemicals must be precisely controlled to ensure efficient precipitation without causing unnecessary chemical additions. The dosing station with iReg piston diaphragm dosing pumps used in Linkenheim-Hochstetten adapts the chemical amount to the conditions in the wastewater flow. The chemical output depends on the phosphate concentration in the wastewater.
Two functions are available in automatic mode for the piston diaphragm dosing pumps with iReg intelligent control:
– Batch operation with specification of the dosing quantity and dosing time
– Flow rate with control of the specified dosing output in litres per hour via internal measurement or external flow meter
This allows the quantity of required chemical to be precisely determined and precipitant consumption to be optimised.
The dosing pump has a ProfiBus DP interface which is used to communicate with the DCS.
This means that the precipitant dosing can be precisely adjusted to the phosphate concentration and the precipitant costs can be minimised.
Sustainable and efficient wastewater treatment
The Linkenheim-Hochstetten wastewater treatment plant is demonstrating its commitment to sustainable wastewater treatment by modernising its phosphate elimination system. This modernisation underlines the municipality’s ongoing efforts to protect the environment and at the same time improve the efficiency of wastewater treatment.
The CONTINUFLOC polymer preparation system with BIG BAG discharge station adapts to limited space conditions
Project location:
Stuttgart-Möhringen (Germany)
Date:
2022
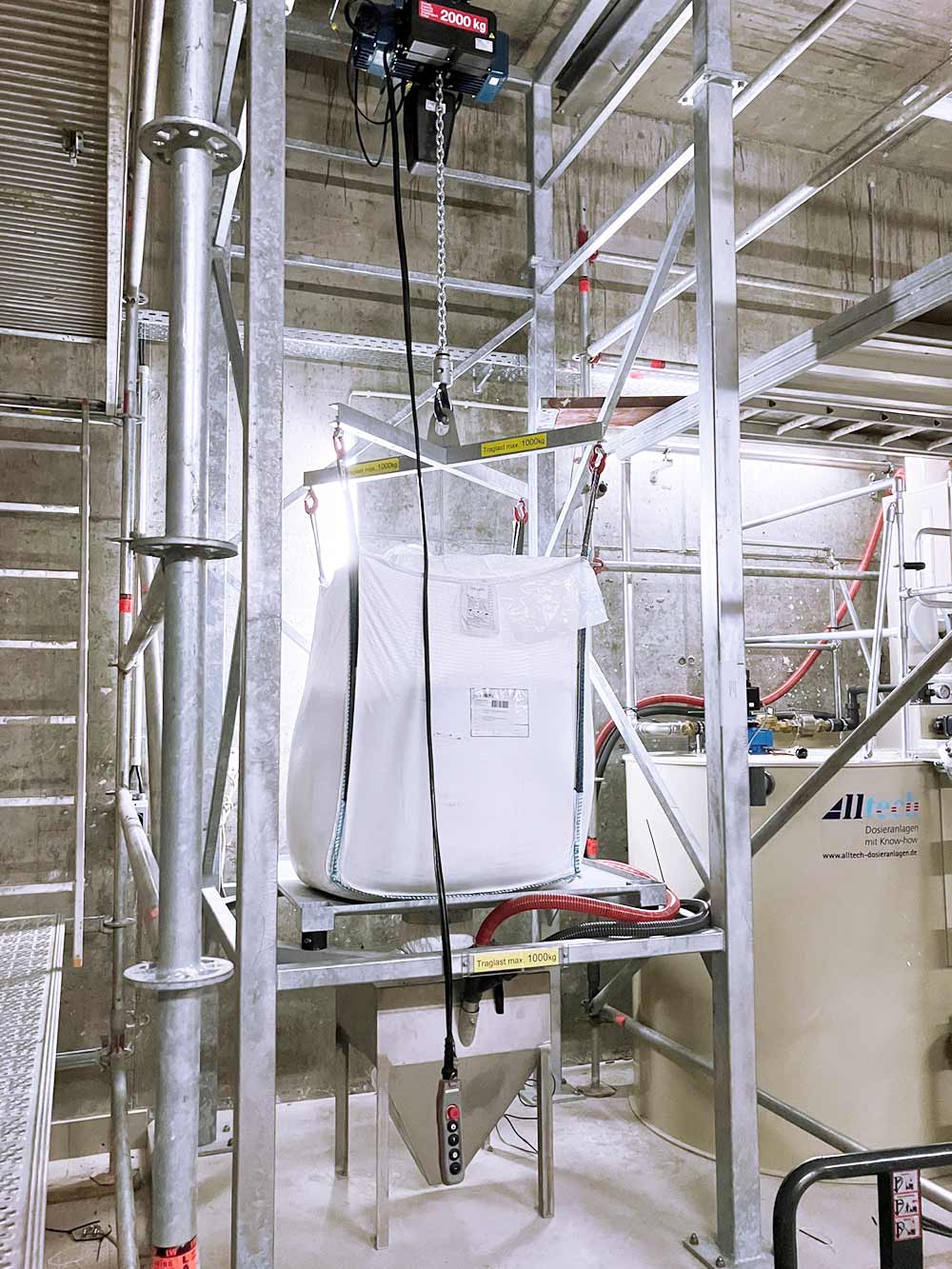
Big Bag unloading system for powder polymer
System used:
Polyelectrolyte make-up system CONTINUFLOC for powder polymer with safety-access and AIRLIFT for pneumatic conveying of powder, BIG- BAG unloading system, solution dosing station and secondary dilution
Description:
What does not fit, is made to fit. The CONTINUFLOC polymer preparation system with BIG BAG discharge station adapts to the limited space conditions in the existing machine building of the Stuttgart Möhringen wastewater treatment plant. In the wastewater treatment process at Möhringen the CONTINUFLOC solution and dosing system for polymer powder is used to improve the mechanical dewatering of excess sludge.
The sludge is mixed with the prepared polymer solution, fed to a centrifuge and dewatered there, to then be fed to sludge digestion and drying.
Ready for polymer processing
The polyelectrolyte powder used to dewater the excess sludge is delivered in big bags and unloaded via the discharge frame with integrated lifting crane. From the feeding hopper, the polymer powder is pneumatically lifted into the storage hopper on the automatic two-chamber pendulum make-down system CONTINUFLOC by means of the AIRLIFT conveyor. The make-down system is supplied ready for operation, wired, piped and electrically and hydraulically factory tested. At the customer’s request, the piping of the system was completely made of PPH.
Control of the system via S7-1200
Via the robust, high-resolution color touch panel, the operators at the Möhringen wastewater treatment system can read out different informations regarding the settings, operating hours, or list the alarm history of the system, to obtain an overview of the system status at any time. The powder dosing is also controlled via the touch panel and the make-down concentration can be set directly at the system or via DCS. Communication between the system and the DCS is done via a Profinet interface. The position of the control panel was adapted to the special space conditions in the machine building to allow a good visibility and ergonomic operation of the system.
Safety access system enables safe operation and maintenance
With the accessibility package, which consists of an access stairway with two handrails, a railing system with safety door and the platform with grating on top of the solution tank, the wastewater treatment plant personnel have safe access to all parts that need inspection and maintenance. This is important for the safe operation of the system.
Dosing station for the prepared polymer solution
The prepared polymer solution is dosed to the injection point in the sludge line by using eccentric screw pumps and a secondary dilution system.
Dosing station and CONTINUFLOC V9 optimise the wastewater treatment of the WWTP Groß Düngen (Germany)
Project location:
Groß Düngen, Salzdetfurth (Germany)
Date
2019
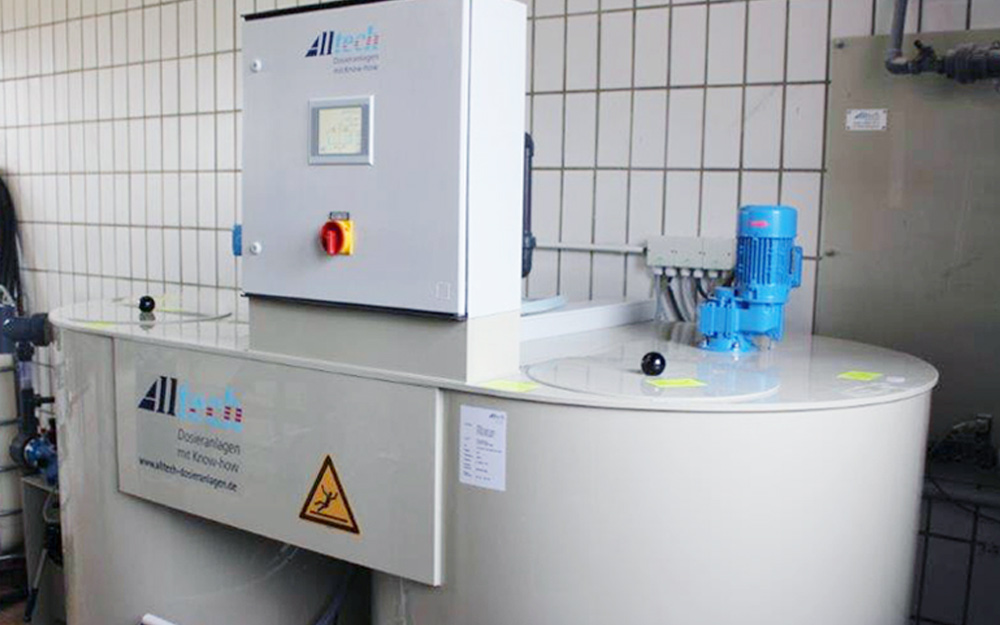
CONTINUFLOC solution preparation system
System used:
Dosing station and preparation system CONTINUFLOC V9
Description:
The city of Bad Salzdetfurth has invested heavily in the final expansion of the wastewater treatment plant Groß Düngen. For example, a second sewage line with all necessary machinery and plant components with activated sludge tanks and secondary clarification tanks was built. The existing machinery and equipment in the wastewater treatment plant had to be renewed, enlarged and rebuilt to ensure future wastewater treatment.
The full automatic CONTINUFLOC V9 polyelectrolyte preparation system has been designed to give the optimum preparation process for most common flocculants
Optimal product mixing enables polymer savings up to 20% compared to flow-through systems. The SIMATIC S7-1200 is used in the new V9 version. Together with the TIA Portal, these controllers offer new and efficient possibilities for programming and configuration. Communication of the CONTINUFLOC V9 control with the DCS (distributed control system) is optionally possible via Profibus DP or Ethernet. This allows the complete monitoring in the DCS. The CONTINUFLOC systems are excelling in easy operation, high reliability and safety. Particularly noteworthy is the graphic display of the process P&ID on the touch panel. By this the status of the system as well as the modus of each drive and sensor are made visible at a glance.
The PLC allows easy, detailed diagnosis
The intuitive operation of the CONTINUFLOC V9 preparation and dosing systems is done via the color touch panel. The control of the V9 has enough memory to store all alarm messages for a long period of time. If an error occurs, it can be quickly seen in the list. The data stored here can also be saved on an external storage medium (SD card). The recording of relevant system parameters and their display in charts for troubleshooting is possible in the background. Software updates can be made via the USB interface.
Better polymer mixing and less wear
The redesign of the dosing and maturity chambers gives an optimized flow and circulation of the prepared solution. This ensures the optimum effectiveness of the agitators. The new design of the agitators give improved polymer mixing, while increasing the energy efficiency according to IE3 standard (from 0.75 kW). The improved agitator bearing at the bottom of the tank ensures a smooth run and reduces wear. A reengineered product distribution channel enables reliable operation and reduces cleaning intervals. Operational safety is further enhanced by the use of a corrosion-resistant dosing hopper with inspection window for the powdery product. By using a new dispersion and wetting device, the flocculant is optimally wetted and better dissolved.
Additional control and monitoring functions
The level measurement is done via robust and reliable pressure sensors with analog output and optical level display on the V9 touch panel. Monitoring functions for a liquid (neat) polymer dosing pump with flow or overpressure monitoring can be integrated optionally. A powder conveyor from the AIRLIFT series can be selected for the automatic feeding of the powder hopper (option). With the CONTINUFLOC V9, the high-performance mixing system EMMI can also be used for special liquid polymers. The new control can be extended to control also one solution dosing pump with secondary dilution and a solution buffer tank with agitator and continuous level measurement.
Modernization of the WWTP Groß Düngen
Among the newly used systems in Groß Düngen is the CONTINUFLOC 2000 V9-1 FGR for preparation from liquid polymers. The installed polymer preparation system will supply 950 l / h of prepared solution at 45 minutes maturation time. The neat polymer dosing station is equipped with the dry-run-proof piston diaphragm dosing pump FKM and controlled from the CONTINUFLOC V9. The aim of the expansion and modernization was to improve the cleaning performance. In addition, energy savings and savings of chemicals have been achieved.
Modernization of the wastewater treatment plant Erlensee ensures compliance with strict discharge values
Project location:
Erlensee (Hesse)
Date
2017/18
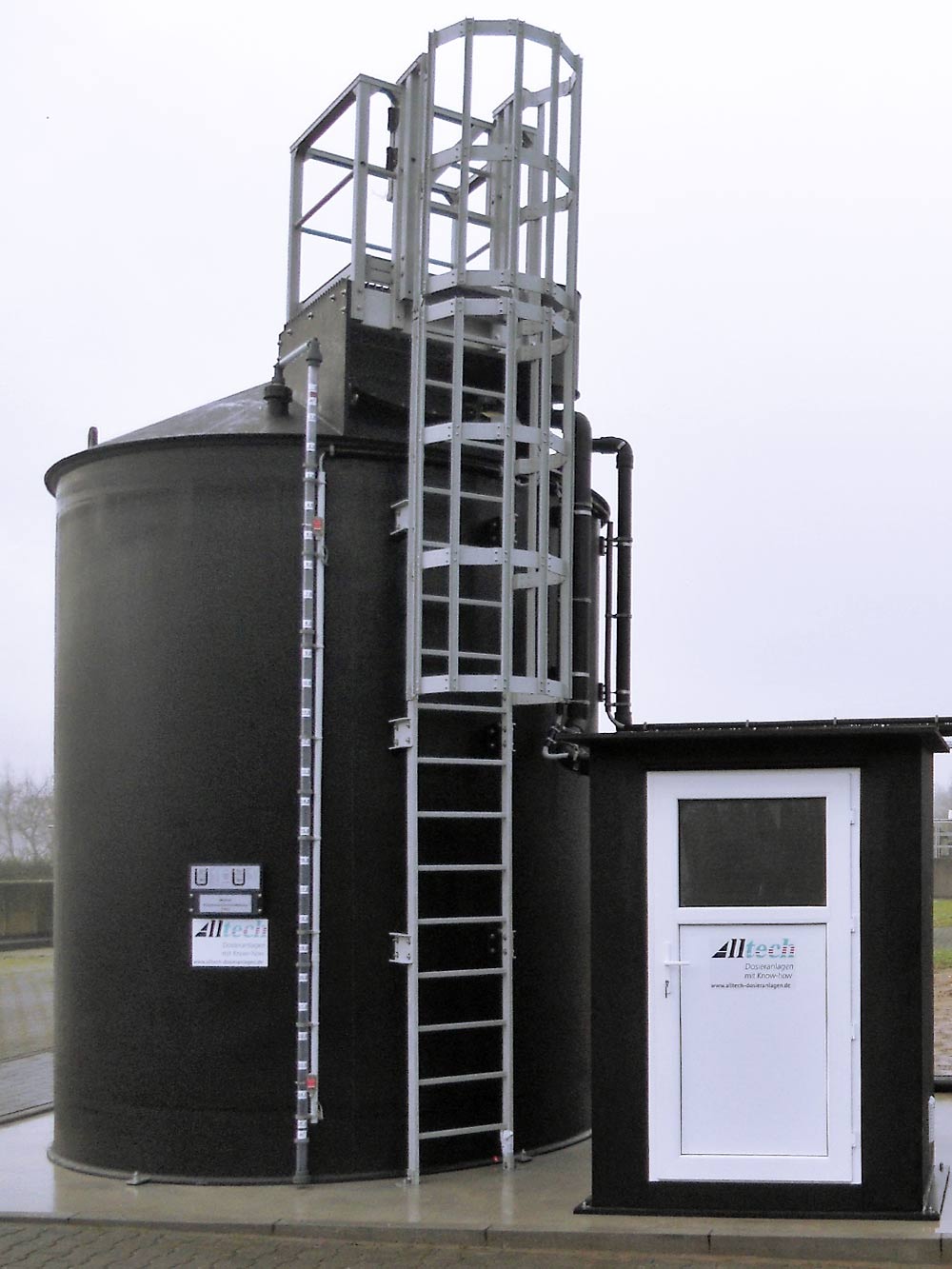
Storage and dosing system for phosphate elimination
Anlageneinsatz:
Phosphate elimination system with safety and monitoring devices, dosing station in protective cabinet made of PE, preparation and dosing system CONTINUFLOC for liquid polymer concentrates.
Beschreibung:
With the modernization of the waste water treatment plant Erlensee, the city of Erlensee is taking an effective measure to improve water protection.
Modernization of the treatment plant allows compliance with the stricter discharge values
The modernization of the Erlensee wastewater treatment plant must be seen in the context of the implementation of the strict guidelines of the European Water Framework Directive for water protection. One aim of this directive is to improve the quality of surface waters. With the improvement measures that have been taken, the strict legal requirements for discharge values of the treated wastewater into the river Kinzig can be reliably met.
New phosphate elimination with storage tank and dosing station for outdoor installation
Assembly and commissioning of the new phosphate elimination station was completed in February 2018. The insulated storage tank with PE safety bund is used for storing 25m³ acidic and alkaline precipitants and flocculants of all hazard classes in accordance with the requirements of the Water Resources Act and the VAwS. Storage tank and safety bund have the approval of the DIBt (Deutsches Institut für Bautechnik). The storage tank is equipped with overfill protection, leakage sensor, ventilation and level indicator.
Safe access to the storage tank facilities is ensured by vertical ladder with safety cage and platform constructed according to accident prevention regulations.
Cabinet made of PE protects operating personnel and dosing station from weather influences
The dosing station is equipped with two piston diaphragm dosing pumps with a maximum dosing capacity of 28l / h (one dosing pump in-duty, one dosing pump stand-by) and serves to deliver polyaluminium chloride solution. The UV-resistant PE protective cabinet is walkable. Heating, lighting and ventilation are contained in the protective cabinet, so that the operating personnel have access to the dosing station well protected from weather conditions.
The PROCON dosing output control system optimizes precipitant consumption and significantly reduces the need for chemicals.
Preparation of liquid polyer concentrate with the two-chamber pendulum system CONTINUFLOC
As part of the modernization process, the polymer concentrate reprocessing and dosing system in excess sludge thickening was also renewed.
This is where the CONTINUFLOC two-chamber pendulum system is now used, which is characterized by optimum concentrate mixing and maximum efficiency for reduced chemical consumption.
Our single source philosophie
Alltech has carried out this project from planning to production, installation and commissioning. The on-site TÜV inspection was also accompanied and the employees of the wastewater treatment plant were thoroughly trained in operating the entire dosing system.
Installation and commissioning of the new phosphate elimination system at waste water treatment plant Windisch completed
Project location:
Windisch (Switzerland)
Date:
2016
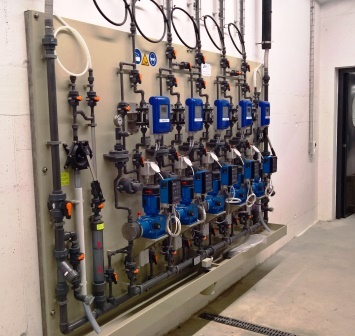
Dosing system on wall mounting plate
System used:
Storage and dosing system for flocculation agent and CONTINUFLOC solution and dosing systems
Description:
for phosphate elimination Alltech uses a storage and dosing system for iron chloride sulphate
Expansion of ARA Windisch required a new concept for phophate elimination
In the WWTP Windisch (Switzerland) waste water for 12 connected municipalities is treated. With the new municipalities of Turgi and Untersiggenthal, the plant in Windisch will now clean the waste water for a population of up to 90,000 equivalents. Alltech received the order to supply, install and commission the phosphate elimination system as part of the expansion of WWTP with additional biofiltration. The WWTP Windisch also uses three Alltech CONTINUFLOC solution and dosing systems in the sludge dewatering process.
Phosphate which is contained in the waste water is removed by chemical precipitation
The waste water is treated in 6 steps (bar screening, grit chamber, pre-treatment, biological treatment, phosphate elimination and secondary clarification) and is then discharged into the river Aare.
The expansion of ARA Windisch on biofiltration required a new concept for phosphate elimination. The tank filling, flocculation agent storage and dosing station were built in the new biofilter building with limited room height. Iron chloride sulphate is used as flocculation agent, but it is also possible to switch to other chemicals by means of two independent storage tanks.
Storage and dosing station according to the local regulations of water protection
In general, systems for fluids hazardous to water are subject to the Swiss regulation VWF (Verordnung über den Schutz der Gewässer vor wassergefährdenden Flüssigkeiten). This corresponds to the water protection regulations of the German Water Resources Act (WHG). By this the components had to comply with the relevant SUVA directives and the technical tank regulations (TTV Switzerland) as part of the project specifications.
The cylindrical storage tanks are designed according to VWF and have a net volume of 26 cubic meters.
The tanks are filled with the flocculation agent from the tank lorry by means of the automatic tank filling unit TABESY. Both storage tanks are equipped with continuous level control and overfill protection. The storage tanks were installed in a specially coated concrete collecting bund, which is equipped with leak detector.
The dosing station for flocculation agent consists of five dosing lines, which have been completely mounted on a PP wall mounting plate with collecting bund. The robust piston-diaphragm dosing pumps FKM with continuous and linear capacity adjustment, controllable drive motor and integrated safety valve are used here. The dosing pumps are operated by the proportional control TRIGGOMAT C2. The protection of the environment against chemical leaks is ensured by having a collecting bund with integrated leakage detector.
The dosage of precipitant is controlled separately for each dosing point, and for each application point a separate dosing pump is assigned.
Design of all components with regard to the efficiency of the whole plant
In addition to the long service life of all components and operational safety, the customer was particularly interested in optimising the design of every component with regard to the function of the entire plant. The fact that Alltech’s phosphate elimination systems meet these requirements has already been proved in the more than 15-year-old trouble-free operation of the first phosphate elimination system also supplied by Alltech.
Water Treatment in the Wildlands Adventure Zoo Emmen
Project location:
Emmen (the Netherlands)
Date:
2015
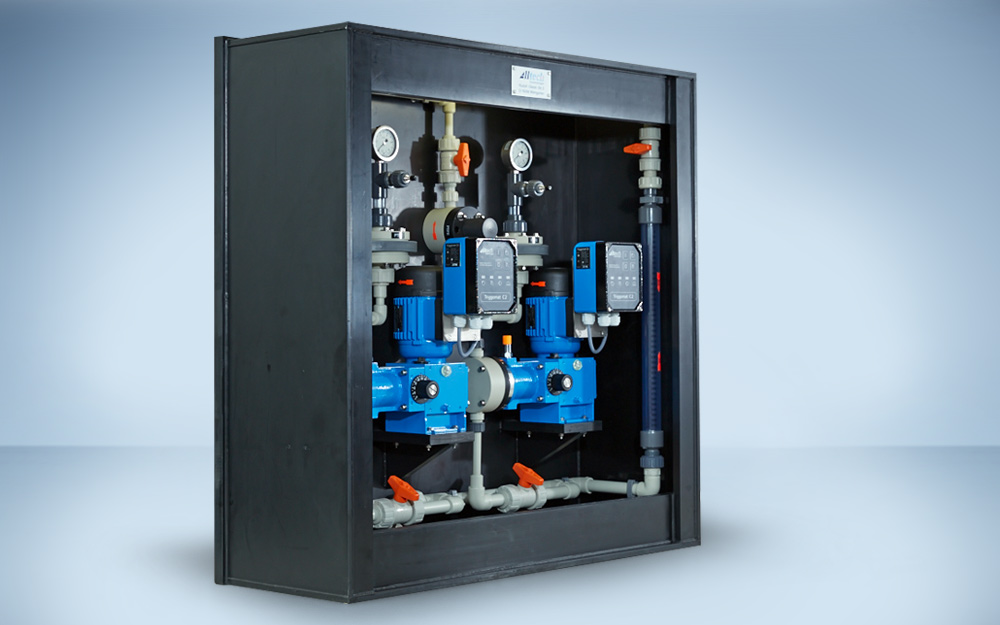
Dosing System in Protective Cabinet
System used:
Dosing system for polyaluminium chloride
Description:
for the flocculation of suspended solids and turbidities Alltech uses a dosing system for polyaluminum chloride.
Clean water in the Wildlands Adventure Zoo Emmen
The Wildlands Adventure Zoo Emmen, a 22 hectare wildlife and theme park, will open in March 2016.
In this Adventure Park – among other theme worlds – the polar environment is presented in a separate area. There live sea lions, penguins and polar bears. The natural environment is simulated by rocks, pine trees and extensive water areas.
In order to keep this water clean and clear, dosing systems by Alltech are used for PAC-dosing. Polyaluminum chloride serves as flocculant.
In flocculation impurities in water are coagulated in order to then remove them more easily.
The scope of delivery includes dosing station with piston diaphragm dosing pumps FKM and proportional control TRIGGOMAT C2
The dosing station was fully assembled by Alltech on a mounting skid and installed in a protective cabinet with transparent sliding doors. Thus, the operating personnel and the environment are well protected against the contact with the chemical in case of leakage.
For chemical dosing the robust and proven piston diaphragm dosing pumps FKM are used.
All dosing pumps of the FKM series are equipped with a TÜV certified pressure relief valve as standard (integrated in the hydraulic system of the pump).
The dosing pumps are infinitely linearly adjustable in the range 0-100%.
The proportional control TRIGGOMAT C2 controls the drive motor of the dosing pumps. In automatic mode, the pump is operated depending on an analog input signal.
Chemical dosing – well designed and equipped for maximum safety
Project location:
Rotterdam (the Netherlands)
Date:
2015
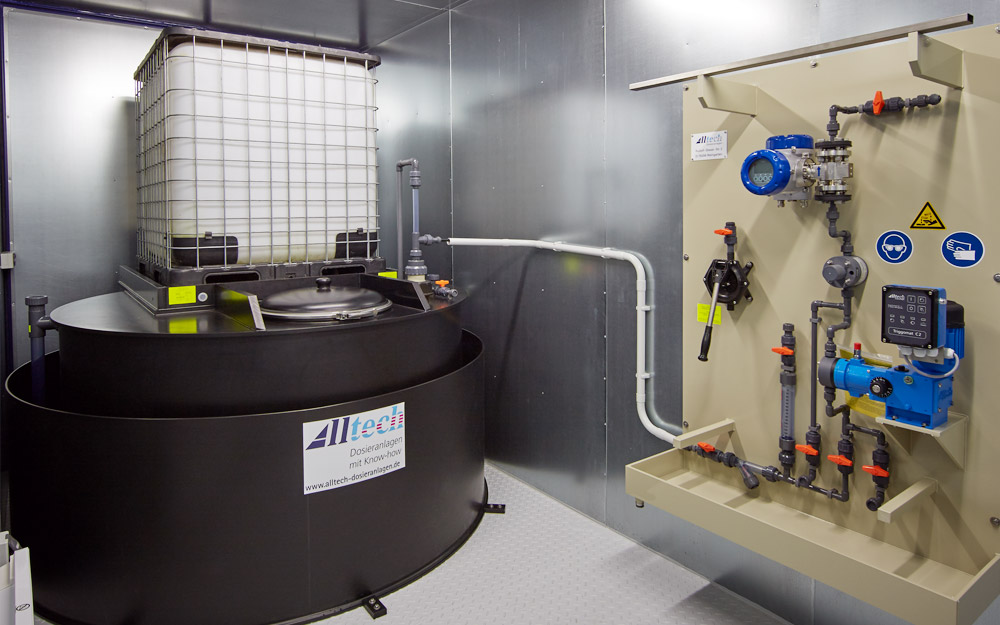
Dosing station for PAC, built in a container
System used:
Dosing system for polyaluminium chloride
Description:
For the wastewater treatment of a large refinery a tailor-made solution for the dosing of polyaluminium chloride was required.
Alltech Dosieranlagen engineered for this customer the complete package – from design to manufacturing and installation of the dosing equipment in a container.
Security, flexibility and ease of operation were the three major requirements that Alltech had to observe in this project. The dosing system of polyaluminium chloride (PAC) will be used in the wastewater treatment plant of the oil refinery. Based on customers specifications Alltech developed a special solution, which contains the complete chemical dosing package including mother tank, built in a 20’ high cube container.
Use of a 20’ high cube container
The container solution offers many advantages. First, for example, no building works must be carried out on the premises of the refinery. This ensures that the application site remains flexible. The high cube container offers enough room for the entire dosing station and mother tank.
Continuous supply, simplified monitoring
The mother tank is used for safe installation and discharge of standard IBCs and is equipped with a collecting bund. The German Institute for Building Technology (DIBt) granted to the mother tank of Alltech an authorization under the aspect of safety. Using a forklift, the IBC is positioned directly on the tank and then completely emptied into this. Having a chemical amount of 10 to 50% left in the mother tank the refilling with a new IBC is possible. Hereby a continual supply of the dosing system can be ensured and the timing of the transfer does not require continual monitoring.
For the application in the refinery Alltech has equipped the dosing station with a removable splash guard. This protects the operating personnel additionally from contact with chemicals. An important customer requirement was also the usability of the system. To accomplish this, Alltech equipped the dosing station with flush connection, calibration cylinders and magnetic flowmeters. A total package that allows easy and safe handling and maintenance of the System.
Pilot project for the elimination of micro-pollutants
Project location:
Sissach (Switzerland)
Date:
2014
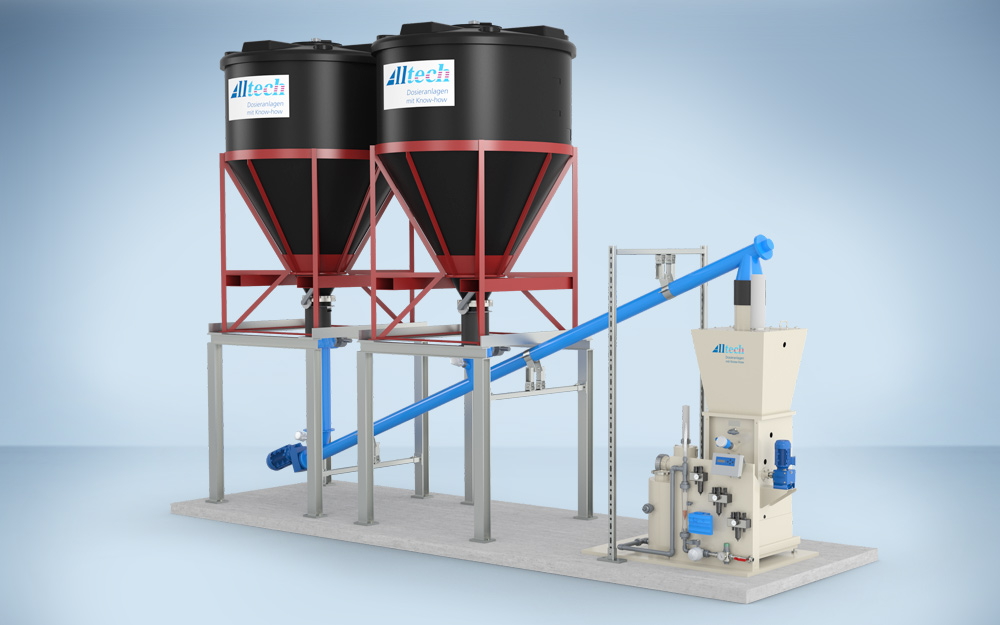
Dosing system for activated carbon
Systems used: :
Complete dosing system for activated carbon
Description: :
In many wastewater treatment plants investments will be made in the coming years to introduce the so-called fourth purification step for the removal of micro-pollutants: The Alltech Dosieranlagen GmbH has designed and manufactured a preparation and dosing system for powder activated carbon on a pilot project for the elimination of micro-pollutants in the wastewater treatment plant ARA Ergolz 1 in Sissach (Switzerland).
Despite several purification steps in waste water treatment plants micro-pollutants like residuals of painkillers, artificial sweeteners, pesticides or caffeine remain in the treated wastewater. These residuals reach rivers and lakes (surface water) via the treated wastewater. Since drinking water is also made using surface water, the micro-contaminants return into the food chain. To avoid this, in the coming years investments will be made in many wastewater treatment plants to introduce the so called fourth purification step.
TREATMENT OF MICRO-POLLUTANTS WITH ACTIVATED CARBON
In order to remove these micro-pollutants from wastewater, there are actually two treatment approaches: the powder activated carbon method and ozonation. In the case of the approach with powder activated carbon, the powder activated carbon is brought into contact with the waste water. The micro-pollutants attach to the surface of the activated carbon particles and are filtered afterwards. Alltech has designed and manufactured a preparation and dosing system for powder activated carbon for the pilot project on the ARA Ergolz I.
SYSTEM FOR THE PREPARATION OF A POWDER ACTIVATED CARBON SUSPENSION
The system for the preparation of powder activated carbon suspension consists of the PAC storage with interchangeable containers, screw conveyor, powder feeder, dosing and wetting system and ejector for suspension feeding. Two interchangeable containers, filled by the PAC supplier with powder activated carbon, are positioned over a screw conveyor and feed alternately via an automatic switch the conveyor screw. Each container has a volume of 2,700 liters. Through the use of a duty and stand-by arrangement the continuous supply of activated carbon is ensured and the handling of empty containers can be done while the system continues to work from the second container. A conveyor screw feeds the powder feeder with activated carbon. To get an accurate dosing, the powder feeder is positioned on a scale that controls and monitors the accurate powder addition. In the special wetting unit, the activated carbon is dispersed with water and then fed via an ejector into the process.
Neutralisation system for mountain water.
Project location:
Bad Wildbad
Date:
2013
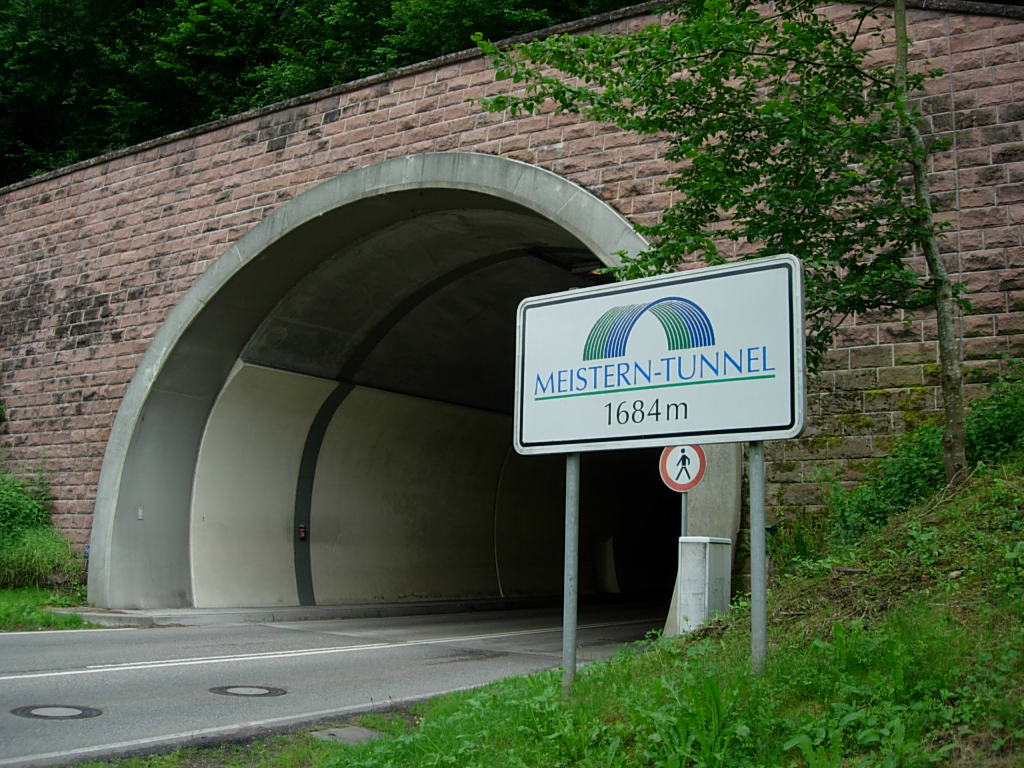
Systems used: :
Continuous neutralization system, chemical storage tanks with necessary dosing and monitoring equipment and electric control
Description: :
In Bad Wildbad, Baden-Wurttemberg the 1,684 m long Meisterntunnel is currently being restored in the scope of the retrofit programme for national road tunnels. The aim is to bring the construction (opened in 1997) up to the newest technical standard and to meet the increased demands on the safety and ventilation standards. The tunnel restoration is being planned and implemented by Karlsruhe district council. A neutralisation system from Alltech Dosieranlagen is a part of the retrofitting measures for the new Meisterntunnel.
NEUTRALISATION PLANTS IMPORTANT FOR THERMAL WATER AS AN ECONOMICAL FACTOR.
In the course of the first construction phase (retrofitting), Alltech Dosieranlagen renewed already existing system that is also designed for the second construction phase (construction of a parallel emergency tunnel from summer 2014). The job of the neutralisation system is to prevent that drinking and thermal water are contaminated. As Bad Wildbad is a protected zone of mineral spas the significance of the thermal water not to be underestimated, in addition the environment, economic factors also play a role. The system to neutralise the mountain water includes in addition to the continuous flow neutralisation system also chemical tanks with the corresponding dosing technology and control equipment.
REDUCING THE PH-VALUE TO 7.5
The installation of the system is in underground shafts next to the tunnel. If mountain water seeps into the tunnel, it penetrates the freshly installed concrete. Through this alkaline substances enter the water and increase the pH value. If this water was to flow into the river Enz, it would endanger animals, plants and the whole environment. With the aid of the neutralisation from Alltech Dosieranlagen, mountain water seeping into the tunnel is collected, the pH value is reduced to 7.5 and then flows into the Enz. The plant runs fully automatically and started operation in September 2013 for at least the next 10 years. First then will the new concrete be washed enough for the pH value to have a neutral impact on the environment.
Restoration and expansion of a sewage treatment plant.
Project location:
Zermatt
Date:
2013
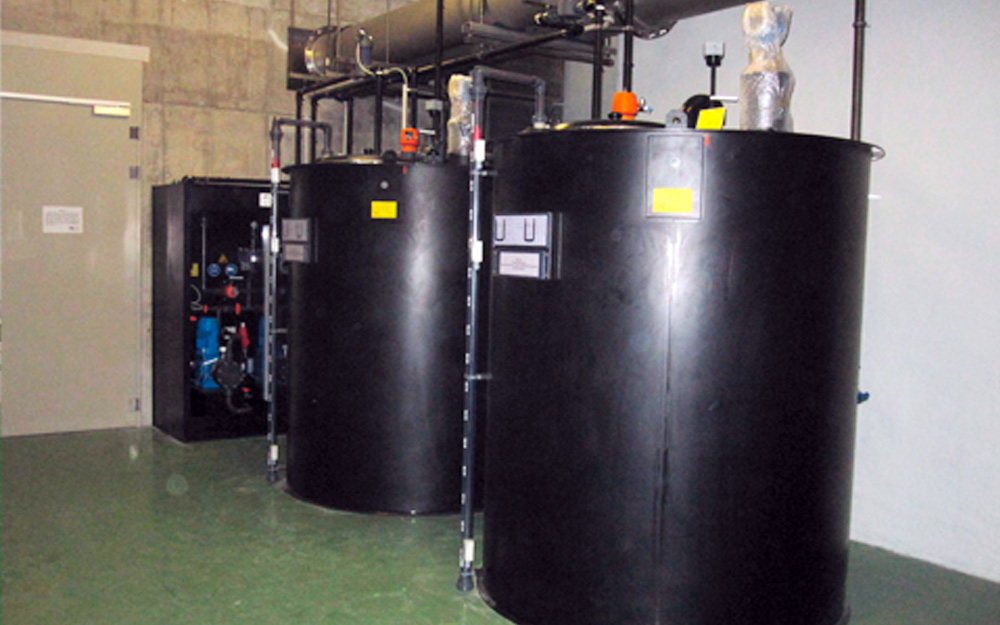
Systems used: :
Chemical tank with collecting basin and dosing station for sodium hypochlorite/bleach, chemical tanks with collecting basin and dosing station for citric acid, collecting basin and dosing station for sodium hydroxide, CONTINUFLOC 4000 polymer preparation system, piston diaphragm metering pump FKM
Description:
An innovative membrane system to purify sewage began operation in 2013 in Zermatt, Switzerland. Alltech supplied the dosing technology equipment for this project. The sewage plant that have been in operation since 1982 can now through the expansion and modernisation clean the sewage from approx. 60,000 residents. To achieve this activated sludge system was replaced with the more modern membrane technology and expanded by nitrification and denitrification. The planning and implementation of the plant technology was, due to the local conditions, the international spa lies 1, 600m above sea-level, and the tight schedule a particular challenge for Alltech, but which however the company successfully conquered.
CUSTOMISED DOSING TECHNOLOGY FOR SEWAGE TREATMENT.
The operator of the sewage treatment works (STW) Zermatt place particular value on a robust and durable dosing technology as well as reliable functioning. Also due to the limited access: the underground treatment works are built into a cave in the cliff and can only be reached by a mountain road. The sewage treatment is implemented in four phases:
- Mechanical cleansing: Using a raking system undissolved residuals such as textiles or paper are removed from the water. In addition sand and grease separators are utilised.
- Chemical sewage treatment: preparation of the biological clarification process through the addition of flocculants and ferric salts.
- Biological treatment: remaining organic contaminants are dissolved by micro-organisms.
- Sludge treatment
THE SOLUTION: ROBUST AND DURABLE PLANT TECHNOLOGY.
In order for ARA to also make the tourist area usable for 60.000 residents, the active sludge process was replaced with the more modern membrane technology process and expanded by nitrification and denitrification. Alltech supplied the dosing technology equipment for the membrane technology process. The new storage and dosing stations will be used for cleaning the membrane, elimination and flocculation:
- Chemical tank with collecting basin and dosing station for sodium hypochlorite/bleach
- Chemical tank with collecting basin and dosing station for citric acid
- Chemical tank with collecting basin and dosing station for sodium hydroxide
- and CONTINUFLOC 4000 polymer preparation system.
In order to meet the high quality and safety requirements, Alltech exclusively used cylindrical tanks with certificate for Zermatt. The models manufactured of PE have both the „general construction approval“ from the DIBt (German Institute for Construction Technology) and therefore comply to the standards prescribed in the Water Resources Act, as well as product testing certification KVU from the SVTI (Schweizerischer Verein für technische Inspektionen) and are equipped with all safety technology relevant components.
For a particularly high level of operating safety, Alltech always considers the different properties of the chemical used in designing and producing the storage and dosing stations. This includes the testing of the chemical properties, the pressure, dosing quantity, control mode and the regulation range. For gaseous substances such as bleach, the use of special components is tested in order to ensure a high dosing accuracy.
THE ADDED VALUE: SYSTEM WITH KNOW-HOW.
Alltech convinced the operators of Zermatt sewage works through the ability to offer a complete solution. This also includes the reliable, durable piston diaphragm metering pumps FKM, with which the sewage works in Zermatt is equipped. The dosing output of the piston diaphragm metering pumps type FKM is linear and continuously adjustable in a range of 0-100 %. In Zermatt smaller pumps with an output of 0-24 l/h and larger metering pumps with an output of 0-1500 l/h were used. The components in contact with the medium are made of PVC, PPH or PVDF; the membranes are of PTFE. All metering pumps in this range are equipped with an integrated overpressure safety valve (TÜV certified). The dosing output is linear and continuous both when the system is in operation or at rest. The dosing pump output is adjustable via an external 4-20 mA signal from the control centre.