References
Paper production
Polymer preparation system, mother tank and dosing stations are part of Vajda’s new tissue production line
Project location:
Dunaföldvar (Ungarn)
Date:
2022
Systems used::
Polyelectrolyte preparation and dosing system CONTINUFLOC V9, mother tank, dosing station for polymer solution and dilution
Description:
Mother tank and dosing stations are used for feeding additives (wet strength agents) in the production process of tissue paper. Dosing of the retention agent in the production process. The neat polymer solution, prepared with CONTINUFLOC V9 preparation and dosing systems, is used for process water treatment.
Mother tanks and dosing stations for the supply of additives (wet solids) in the production process of sanitary paper
Alltech delivered mother tanks and dosing stations to Vajda Papír as early as May 2022 during the course of the first project phase. As part of the production process of the sanitary paper, various additives are dosed whose task is, among other things, to increase the wet strength properties. Additives also serve to improve the retention of solids on the paper machine wire and drainage during the manufacturing process.
The mother tanks supplied by Alltech function as storage and dosing system for the safe and efficient handling of standardized IBCs (industrial bulk containers). These chemotainers are positioned directly on the tank with the help of a forklift truck or an appropriate lifting device and are emptied into the tank completely. The volume of the mother tank permits the emptying of a complete chemotainer with a fluid reserve of 10-50 percent. In this way, a continuous supply to the dosing system is ensured, and the timing of the transfer process does not have to be monitored precisely.
The mother tank is located in a collecting bund, which protects the operating personnel and the production environment from chemicals in the event of a leak. The dosing stations are mounted on a wall mounting plate or floor mounted and are used for dosing chemicals into various process sections of the paper production.
Preparation of neat polymer and dosing of the retention agent into the manufacturing process and for process water treatment
During the paper production, the components, which will later become the paper, are applied to a sieve as a diluted, watery slurry and filtered. This process of filtration is improved and partly accelerated by retention agents.
In a second project phase, Alltech delivered another mother tank and a CONTINUFLOC dissolving and dosage system with EMMI (an electromechanical mixing system to save polymer concentrate), as well as three dosing stations. One dosing station supplies the flotation system (DAF) with a polymer solution for the treatment of process water. The two other dosing stations supply the paper machine with a polymer solution.
CONTINUFLOC systems are fully-automated two-chamber pendulum systems for polymer preparation. For specific applications with an increased requirement, the CONTINUFLOC can also be equipped with an EMMI electromechanical mixing system. This is characterized by an optimum concentrate mixture and, therefore, maximum efficiency. This results in reduced material and resource consumption. The dissolving and dosing system used at Vajda Papír provides a maximum of 4,000 liters of ready-to-use polymer solution per hour.
Polymer Preparation and Dosing Systems for the Production of Hygienic Papers.
Project location:
Al Nakheel, Abu Dhabi
Date:
2017
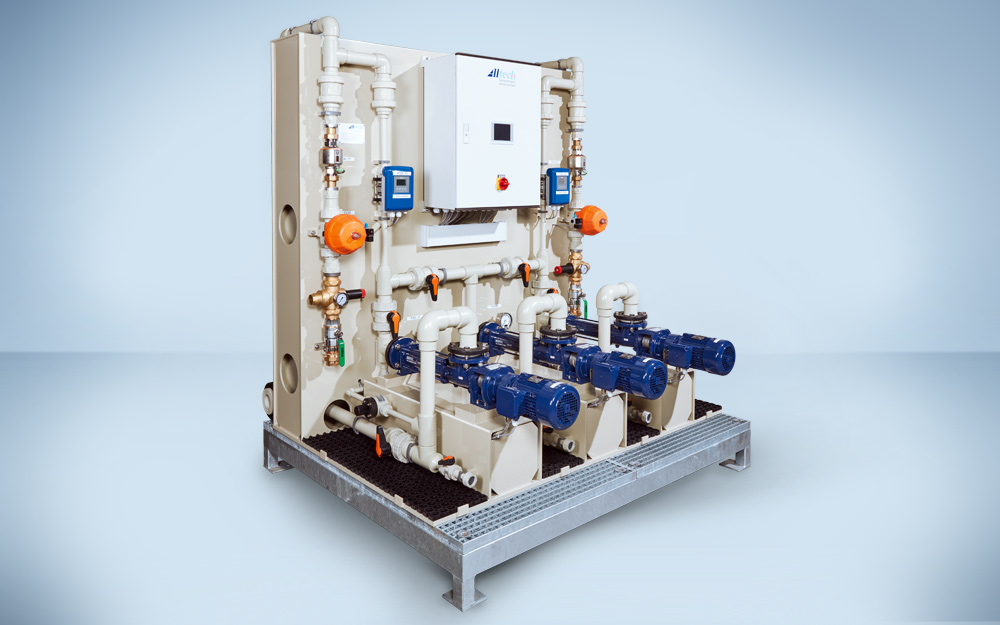
Systems used: :
Polyelektrolyte preparation and dosing systems POLYMAT V8, polymer solution dosing skid and secondary dilution system
Description:
The POLYMAT V8 is a three-chamber-flow-throug system for continuous and discontinuous operation.
Al Nakheel Hygienic Paper Manufacturing Company uses POLYMAT V8 systems for polymer preparation and dosing.
In 2016 Al Nakheel Company started to build a new production facility in Abu Dhabi. The production is scheduled to start in 2017. “The facility is targeting an initial production capacity of 60,000 tonnes per year in the first phase with the potential to double its capacity to 120,000 tonnes per year in the second phase in the coming three to four years.” (http://www.tradearabia.com/news/CONS_305983.html)
Preparation of powdery polymer with polymer solution dosing skid and secondary dilution system.
For the preparation of powdery polymers at Al Nakheel paper plant, the three-chamber flow-through system POLYMAT V8 with powder conveyor type AIRLIFT, polymer solution dosing skid and secondary dilution system are used.
Dosing of additives for optimal wet strength.
With a dosing station suitable for wall mounting, additives are dosed to optimize the wet strength of the hygienic paper.
The application of three-chamber flow-through system POLYMAT is cost-effective and reliable.
The POLYMAT preparation system is a fully automatic polyelectrolyte solution plant, for continuous or intermitted operation, according to the three-chamber flow-through principle.
In standard execution the plant is designed to dissolve powdery or liquid products – a combined use is also possible. Also in Abu Dhabi the plant is delivered completely assembled and tested, with wiring and piping, according to the valid regulations CE, VDE and DIN.
The system essentially consists of a three chamber flow-through tank made of PPH, with agitator crossarms, three inspection openings, drain conduit with valves and overflow, dry material feeder for powder and granulates. The powder is protected against humidity by a thermic protection at the discharge side.
A dynamic mixing system with antifoam feature built-in the mixing chamber guarantees for an optimal dispersion and agitation of the solution.
The switch cabinet uses PLC to control and monitor the complete system. The operation of the system is done by means of a touch screen.
The proportional control of solution water and polyelectrolyte guarantees for a constant solution concentration.
A high quality of the polymer solution is achieved by ensuring an optimal mixing of powder and dissolving water.
DOSING SYSTEMS FOR THE PULP AND PAPER PRODUCTION.
Project location:
Svetogorsk, Russia
Date:
2016
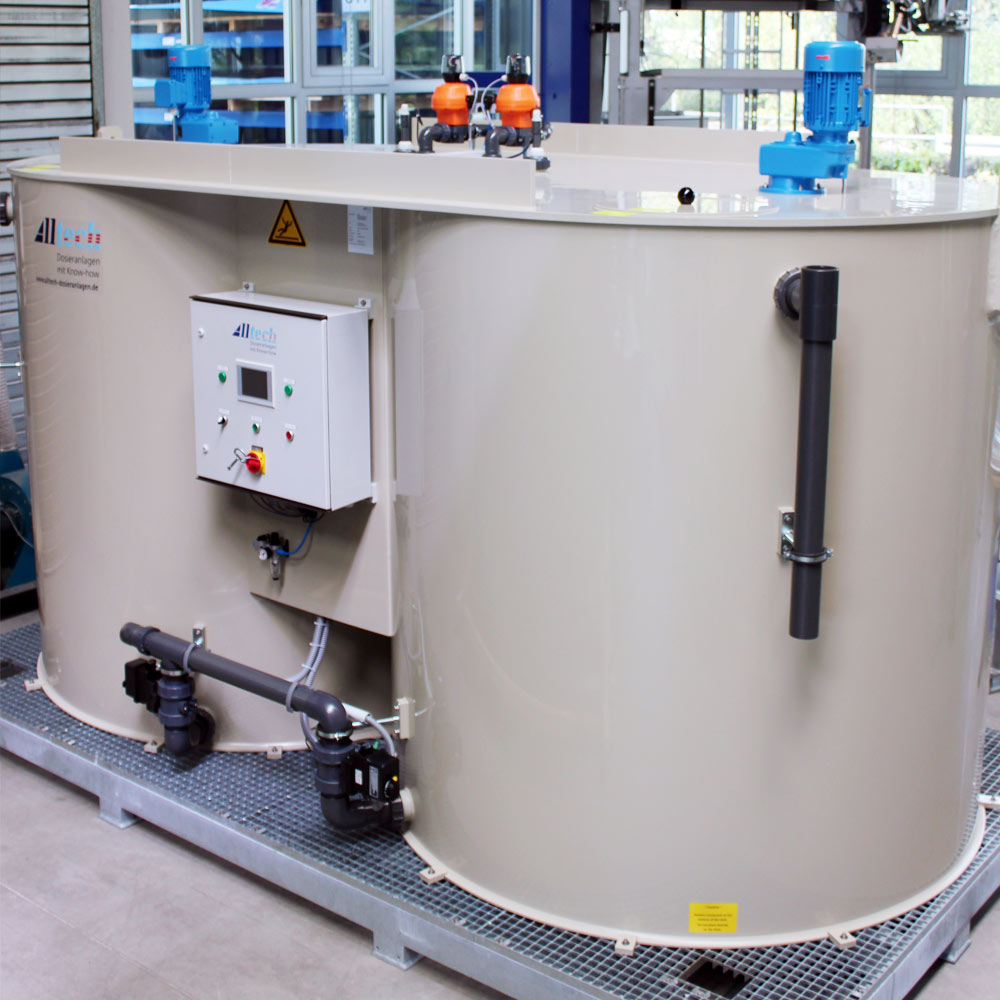
Systems used: :
Twin tank system, dosing system and post dilution
Description:
The twin-tank system is a continuously operating preparation system for liquid polymer.
Twin tank system, dosing station and post-dilution.
Alltech provides for one of the largest pulp and paper production sites in Russia, a liquid polymer preparation system including solution dosing system with post-dilution.
The latest generation of equipment and systems are used here. The 200 hectare area includes three pulp mills, two paper machines and a paper cutting machine for the formats A3 and A4.
Optimum preparation of the product.
The twin-tank system is a continuously operating preparation system for liquid polymer based on a pendulum system of 2 tanks operating in batches, with agitators and automatic filling and discharge switch-over system.
The twin tanks of 2 x 2000 liters capacity are designed for fully automatic operation and continuous discharge of the prepared polyelectrolyte solution.
The produced solution is prepared so that the optimum maturation of the product is ensured using the smallest possible volume.
The storage tanks are made of PP and manufactured according to the regulations of the DVS, the German Association for welding and allied processes e. V.
The twin-tank system has been completely wired and tested in our facilities.
The scope of supply also included the complete dosing skid with post-dilution system and local electrical control panel.
PREPARATION AND DOSING SYSTEMS FOR THE PRODUCTION OF CORRUGATED PAPER.
Project location:
Eisenhüttenstadt
Date:
2013
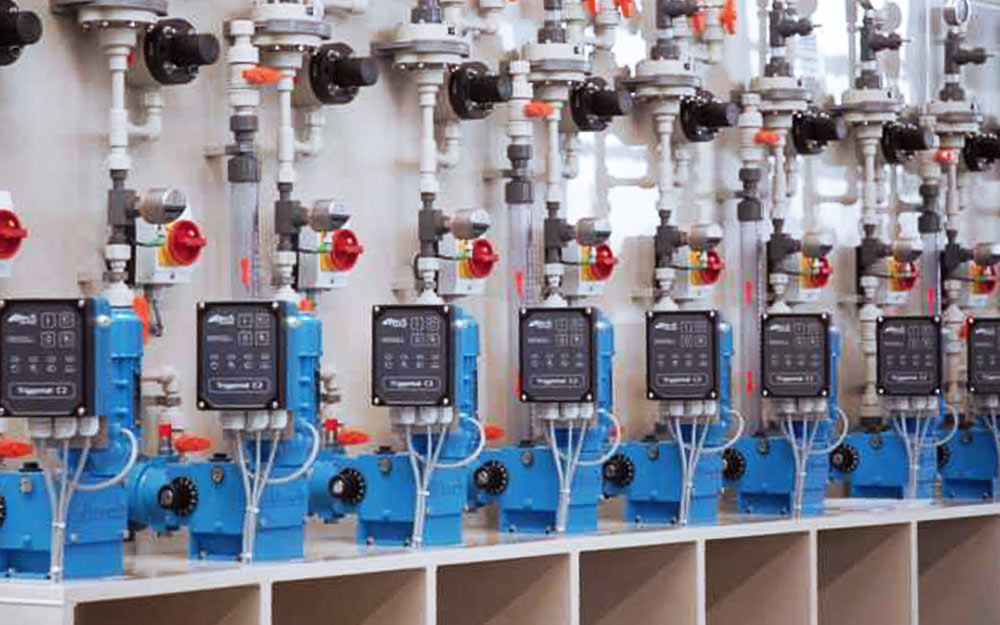
Systems used: :
Polyelectrolyte preparation and dosing system CONTINUFLOC
Description::
For the use of preparation and dosing systems it is important to customers to save resources. Through the optimum product combination and guaranteed maturity time polymer is saved without affecting the efficiency of the process, as the polymer price development is coupled with oil prices, it is expedient to keep this in mind and to use saving opportunities.
OPTIMISATION ALONG THE WHOLE LINE.
Two fully automatic polyelectrolyte preparation and dosing systems CONTINUFLOC with an output of 16,000 l/h (max.) respectively of ready to use polyelectrolyte solution are used in the production of corrugated paper. The full concept of the paper machine is designed for an economical use of raw materials and operating agents. The CONTINUFLOC plants assist in this approach. The precisely dosed polyelectrolyte solution is used as a retention agent for dewatering in the paper machine, this enables a higher performance in the production of corrugated paper, a higher product quality and a lower use of chemicals.
SINK COSTS, INCREASE EFFICIENCY.
With the development of the CONTINUFLOC V8 numerous new features were implemented that opened potential to save costs. The re-designed agitators lead to an improved mixing of polymer while at the same time increasing energy efficiency. New is also the chemical wetting and dilution system that leads to an improved dispersion of the flocculation agent and therefore increase the effectiveness. The impeller positioning at the bottom for the tank ensures a quiet agitation process. The lower strain on the drive and tank lead to less wear. The optimised form of the product addition line does not only improve operating safety but also reduces the need for cleaning.