With dosing systems for chemicals, Alltech Dosieranlagen GmbH provides the essential basis for the treatment of regeneration water and the production of ultrapure water and deionate, and supports customers in the crude oil and natural gas processing industries.
With about 205 million tonnes of oil and 92 billion cubic metres of natural gas, the North Sea is the largest offshore production area. Complex systems are required for the extraction, storage, transport and processing of these important fossil fuels and raw materials. Large quantities of water are required for the majority of these processes. In most cases, however, this is not “ordinary” water, but water that has been specially treated. Very often demineralized water (deionized water) and ultrapure water are used, which are characterized by their chemical composition and the resulting physical properties.
The elaborate methods of water treatment in turn are based on the targeted use of various systems and chemicals that trigger the required processes with precise dosing. With state-of-the-art dosing systems, Alltech Dosieranlagen GmbH enables international customers to precisely dose the required chemicals, thus ensuring safe, reliable and efficient operation of the systems involved.
The customers of Alltech Dosieranlagen GmbH include leading companies worldwide in the field of oil and gas exploration and production.
Example of use of the Alltech dosing pumps
“In a current project, one of our customers, a global player in the oil and gas industry in the northeast of England, is integrating our dosing systems into their system for regenerating ion exchangers,” Ladislaus Bach, Head of Sales at Alltech Dosieranlagen GmbH, explains. “These are indispensable in deionate and subsequent ultrapure water production. Only regular regeneration ensures their function in the long term. Precise coordination of the chemicals used is crucial here, and the simplest and most reliable handling possible for the customer is also of the utmost economic importance, of course.”
46 percent soda lye and 96 percent sulfuric acid are used in the regeneration of ion exchangers and in wastewater treatment. A very wide performance range must be covered for their dosing and supply, which is why the customer required dosing pumps that are as linear as possible as well as adjustable in dosing from 0 to 100%. Only in this way can the pump performance be optimally adapted to the variable process parameters.
Dosing stations for acid dosing by Alltech
In close cooperation with the customer, Alltech’s experts decided to use two dosing stations each for acid and lye dosing. Built into a chemical-resistant protective cabinet made of bimodal polyethylene (PE 100), transparent sliding doors provide maximum splash protection with a permanently unobstructed view of the dosing stations. A tray integrated into the protective cabinet prevents chemicals from escaping and contamination of the production environment in the event of a leak.
The individual dosing stations are equipped with the tried and tested piston diaphragm dosing pumps of the Alltech FKM series. Their dosing capacity can be freely selected and therefore easily adapted to the requirements of process engineering. Here, the pump output is controlled by the SERVOSET stroke length positioning system. By means of a servomotor with integrated position controller and limit switch, the dosing can be adjusted continuously in a linear manner in the range between 0 and 100%. Both local position indication and remote indication via an integrated analogue output are possible.
Optionally, the dosing pump can also be replaced by the FKMi model with intelligent iReg control. iReg controls the pump independently and monitors predefined parameters such as dosing quantity and system pressure. The performance values are displayed, stored and reported digitally.
“Not least, our customer’s success is built on the use of innovative technologies,” Bach adds. “With our sophisticated dosing systems and their individual configuration geared to the specific application, we can make an important contribution to this principle of success.”
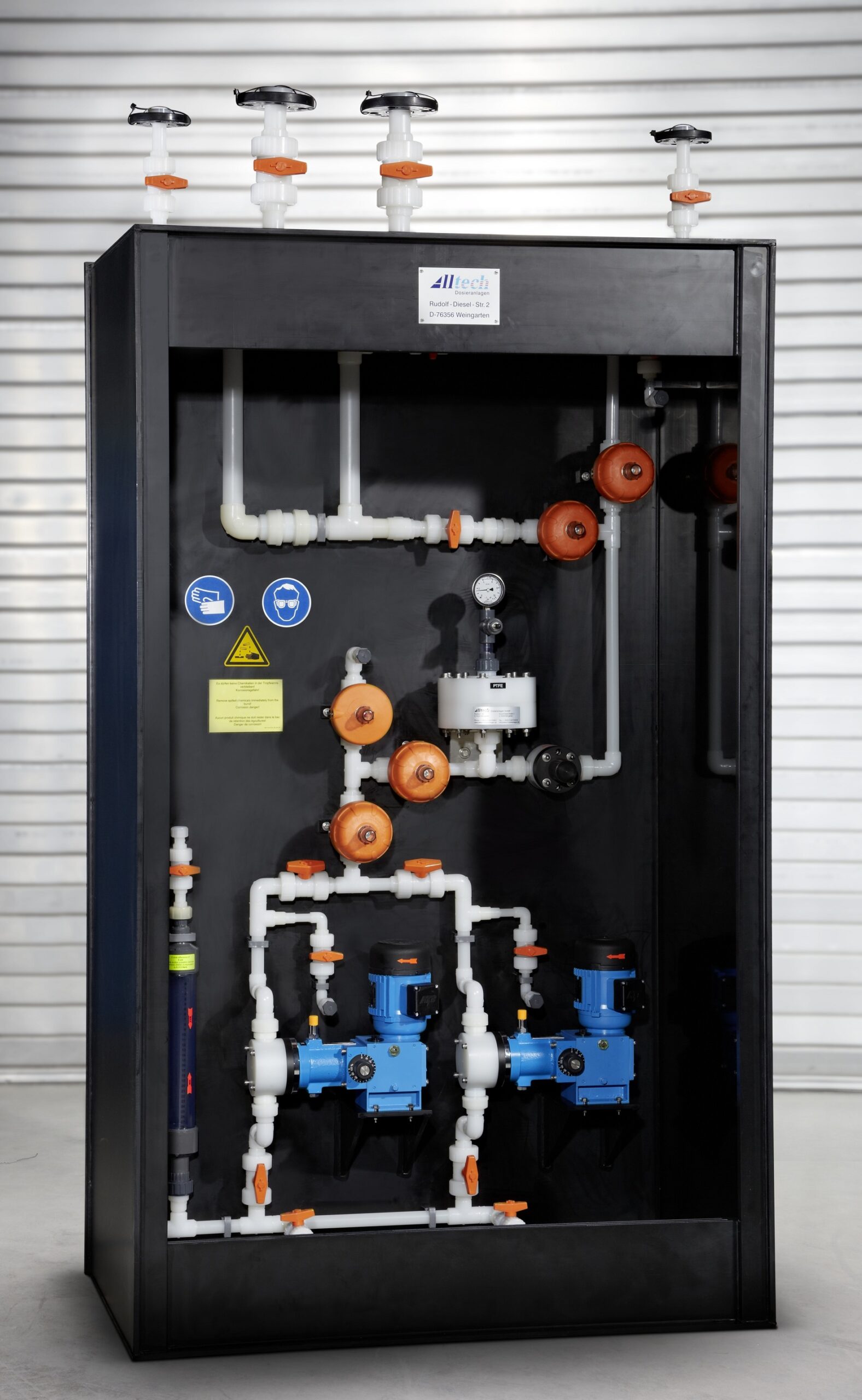